Level 1c | Green Belt Improvement Leader
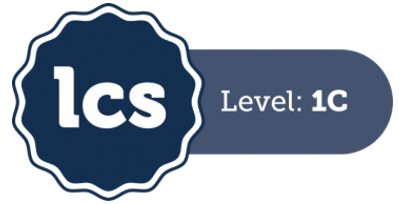
The Improvement Leader Level 1c will build knowledge, understanding, and application of lean improvement and implementation techniques. Candidates that complete LCS 1c will be able to actively participate in improvement activities in the workplace.
Prerequisites for Level 1c (preferable but learning can be incorporated in the course design)
Implementation and improvement tools used to improve and sustain processes
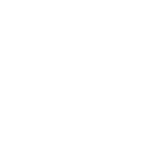
Workplace organisation and optimisation techniques
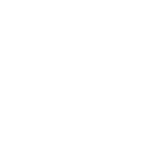
Standard operations

Visual management and performance measures
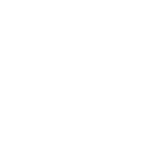
Scheduling, and capacity planning
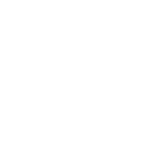
Enablers for flow
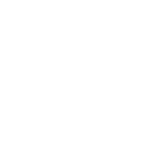
Management and planning
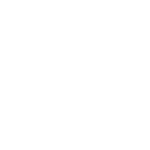
People, teams and sustainability
Delivery
A course or programme designed to deliver Level 1c outcomes can be organised in several ways and there is no prescribed format. It will typically use a combination of:
- Face to face, taught in groups – in modules or blocks of days.
- Digital delivery and eLearning.
- Blended learning
- Workplace based guidance and support – going to the ‘Gemba’.
The total learning time guidance for a course aligned to L1c is 40 hours. This can include face to face teaching, elearning, assessment, pre/post course reading/research, practical application, offline group work, on the job training and one-2-one support activities.
Level Assessment
The assessment shall demonstrate that the outcomes have been achieved.
Knowledge
An assessment that demonstrates the learner can remember and understand L1c Implementation & Improvement, for example, through a multiple choice test, problem or case-based exams, oral exam, essay exam.
Practical Application
The successful Level 1c practitioner shall provide evidence of the application of L1c related tools and techniques in the workplace. Methods that should be used to capture the evidence include A3 reports, project reports, workbook, project portfolio/log or diaries.