There is no doubt that TPM, whichever definition you use (Preventative or Productive) can significantly improve the reliability, longevity and performance of machinery (assets); and those companies that have deployed it effectively have seen significant returns.
Fundamentally, TPM is a series of methods, originally pioneered by Toyota to ensure every machine within a production process can perform its required tasks – so that production is never interrupted.
The definition of TPM I like to use is:-
- Total – Involvement of everyone
- Productive – Maximised equipment effectiveness
- Maintenance – Action to preserve the standard
Terminology – a note of caution
The TPM definition has been a sticking point for many – it has often been seen as the remit of Engineering and not owned by all, yet machine reliability can impact every person in an organisation.
As John Quirke and Andy Brunskill points out in their book TPM: A foundation of Operational Excellence it can cause a them and us mentality – Similar to having a ‘lean guy’, having someone responsible for ‘TPM’ is not inclusive, it is in fact detrimental to the overall programme – A TPM prograamme needs to actively link and compliment your Operational Excellence Journey for your assets and people through leadership.
What is the purpose of TPM
It’s worth reflecting on the five founding principles of TPM developed by S Nakajima; T Suzuki and colleagues at the Japan Institute for Plant Maintenance. These set out why an organisation should deploy TPM.
These are:
- Increase the Overall Equipment Effectiveness (OEE)
- Improved existing Plant Maintenance Systems
- Make Routine asset care part of the job
- Increase Skills (hand and operational, team working and problem solving)
- Early Equipment Management
Our team have also developed a sixth point to add to this:
- Fully Engage your Teams– and ensure the team see the results of their effort, and equally it focuses on the mind on whether you are winning or losing.
Operationally many manufacturers use the WCM (World Class Manufacturing) target of Zero as a desired future state. This means a focus on:
- Zero Accidents
- Zero Defects
- Zero Breakdowns
- Zero Minor Stops
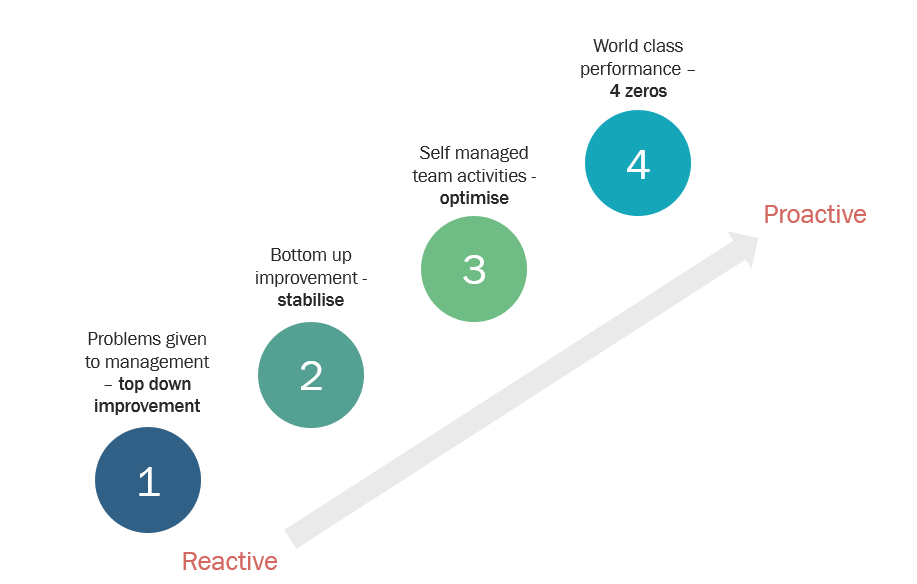
Thinking of deploying or improving your TPM system?
My colleagues and I have developed an 11 Step TPM system to support organisations deploy TPM effectively.
These steps are carefully designed to ensure there is a focus on:
- Measurement
- Condition Appraisal
- Problem elimination; and
- Sustainability
TPM = Today People Matter
At S A Partners we often encourage people to think of TPM as ‘Today People Matter’. In any asset-based enterprise the effective and efficient operation of your assets is a critical factor in the consistent delivery of customer value. Therefore, we can consider our ability to maintain and optimise the performance of those assets as one of the critical systems within a business. As a system therefore it must be designed to support and encourage ideal behaviours of those working within and supporting the asset optimisation system.
Be mindful that TPM does not just focus on equipment but is seen as a philosophy to support improvement. It should be focused on people and establishing the correct relationship between people and their equipment. This will enable ‘ownership’ teamwork and personal development. The key is about unlocking the installed productive capacity of our equipment by unlocking the innovative capability of our people. A simple fact which is regularly overlooked is the users or operators of equipment, machines and processes who can catch the information on the performance of the equipment and prevent it from breaking down. Without securing the teams co-operation and interest no fully effective maintenance or asset care system can be established.
What TPM can do…
Without question TPM deployed well will add value to your customer, your team, and to your organisation. TPM will help you improve OEE, reduce costs, downtime and defects; and when deployed correctly effect your teams engagement, performance and health & safety.
There are numerous case studies on TPM deployment available on our website (www.sapartners.uk/resources), but I have included an example below of a recent activity undertaken and the results achieved over three years:If you are interested in further information about TPM please do contact our me directly or the wider S A Partners team on ku.srentrapasobfsctd@ofni.
Further information
https://sapartners.com/total-productive-maintenance-2/
Useful video’s covering the 11 Step Model can be found here: https://sapartners.com/tpm-11-step/
Also, please do refer to our latest award winning book: TPM: A foundation of operational excellence – available on Amazon here: CLICK HERE